Biodiesel refers to a non-petroleum-based diesel fuel consisting of short chain alkyl (methyl or ethyl) esters, typically made by transesterification of vegetable oils or animal fats, which can be used (alone, or blended with conventional petrodiesel) in unmodified diesel-engine vehicles. Biodiesel is distinguished from the straight vegetable oil (SVO) (aka "waste vegetable oil", "WVO", "unwashed biodiesel", "pure plant oil", "PPO") used (alone, or blended) as fuels in some converted diesel vehicles. "Biodiesel" is standardized as mono-alkyl esters and other non-diesel fuels of
biological origin are not included.

Ford
Focus Bio Ethanol bio fule car
Blends
Blends of biodiesel and conventional hydrocarbon based diesel are products most commonly distributed for use in the retail diesel fuel marketplace. Much of the world uses a system known as the "B" factor to state the amount of biodiesel in any fuel mix: fuel containing 20% biodiesel is labeled B20, while pure biodiesel is referred to as B100. It is common to see B99, since 1% petrodiesel is sufficiently toxic to retard mold. Blends of 20 percent biodiesel with 80 percent petroleum diesel (B20) can generally be used in unmodified diesel engines. Biodiesel can also be used in its pure form (B100), but may require certain engine modifications to avoid maintenance and performance problems. Blending B100 with petro diesel may be accomplished by A. Mixing in tanks at manufacturing point prior to delivery to tanker truck, B. Splash mixing in the tanker truck (adding specific percentages of Biodiesel and Petro Diesel) C. Inline mixing, two components arrive at tanker truck simultaneously.
Origin
On August 31, 1937, G. Chavanne of the University of Brussels (Belgium) was granted a patent for a 'Procedure for the transformation of vegetable oils for their uses as fuels' (fr. 'Procédé de Transformation d’Huiles Végétales en Vue de Leur Utilisation comme Carburants') Belgian Patent 422,877. This patent described the alcoholysis (often referred to as transesterification) of vegetable oils using ethanol (and mentions methanol) in order to separate the fatty acids from the glycerol by replacing the glycerol with short linear alcohols. This appears to be the first account of the production of what is known as
'biodiesel' today.
Applications
Biodiesel can be used in pure form (B100) or may be blended with petroleum diesel at any concentration in most modern diesel engines. Biodiesel has different solvent propereties than petrodiesel, and will degrade natural rubber gaskets and hoses in vehicles (mostly found in vehicles manufactured before 1992), although these tend to wear out naturally and most likely will have already been replaced with FKM, which is nonreactive to biodiesel. Biodiesel has been known to break down deposits of residue in the fuel lines where petrodiesel has been
used. As a result, fuel filters may become clogged with particulates if a quick transition to pure biodiesel is made. Therefore, it is recommended to change the fuel filters on engines and heaters shortly after first switching to a biodiesel
blend.
Distribution
Distribution is possible using today's Petro Diesel infrastructure as long as minor adjustments are
made to both the distribution fueling systems as well as vehicle fuel systems, such as replacement of fuel system, solvent-sensitive o-rings, gaskets, fittings and hoses, filtering of loosened fossil fuel varnishes, prevention and growth of mold and additives to prevent solidification at colder temperatures.
Biodiesels use and production are increasing rapidly. Fueling stations make biodiesel readily available to consumers across Europe, and increasingly in the USA and Canada, and a growing number of transport fleets use it as an additive in their fuel. Biodiesel is often more expensive to purchase than petroleum diesel but this is expected to diminish due to economies of scale and agricultural subsidies versus the rising cost of petroleum as reserves are depleted.
Vehicular use and manufacturer acceptance
Research sponsored by petroleum producers has found petroleum diesel better for car engines than biodiesel[citation needed]. This has been disputed by independent
bodies, including for example the Volkswagen environmental awareness division, who note that biodiesel reduces engine wear. Pure biodiesel produced 'at home' is in use by thousands of drivers who have not experienced
failure. In spite of the fact that biodiesel sold to the public is held to high standards set by national standards bodies, biodiesel has been widely available at fuel stations for less than a decade, and hence is reasonably perceived to carry more risk than older fuels.
Volkswagen, for example, may tell European customers that they have no problem with biodiesel, while dealers in the USA have posted notices that only blends with less than 5% biodiesel are permitted. In 2005, DaimlerChrysler released
Jeep Liberty CRD diesels from the factory into the American market with 5% biodiesel blends, indicating at least partial acceptance of biodiesel as an acceptable diesel fuel
additive. In 2007, DiamlerChrysler indicated intention to increase warranty coverage to 20% biodiesel blends if biofuel quality in the United States can be standardized.
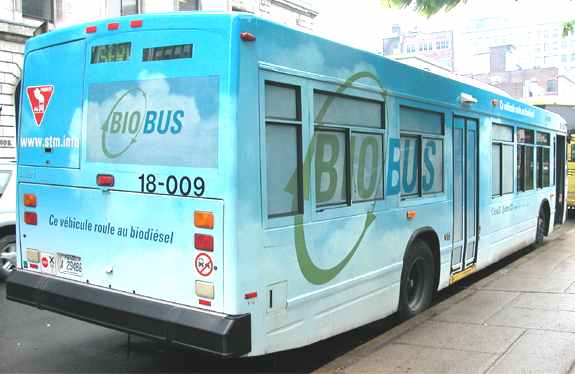
Bio
diesel bus
Railroad use
The British businessman Richard Branson's Virgin Voyager train, number 220007 Thames Voyager, billed as the world's first "biodiesel train" was converted to run on 80% petrodiesel and only 20% biodiesel, and is expected to save 14% on direct emissions.
Aircraft use
Aircraft manufacturers are understandably even more cautious, but some test flights have been
performed and commercial passenger jet testing has been announced by Virgin Atlantic's
Richard Branson.
The world's first biofuel-powered commercial aircraft took off from London's Heathrow Airport on February 24, 2008 and touched down in Amsterdam on a demonstration flight hailed as a first step towards "cleaner"
flying.
Heating oil
Biodiesel can also be used as a heating fuel in domestic and commercial boilers. Older furnaces may contain rubber parts that would be affected by biodiesel's solvent properties, but can otherwise burn biodiesel without any conversion required. Care must be taken at first, however, given that varnishes left behind by petrodiesel will be released and can clog pipes- fuel filtering and prompt filter replacement is required. Another approach is to start using biodiesel as blend, and decreasing the petroleum proportion over time can allow the varnishes to come off more gradually and be less likely to clog. Thanks to its strong solvent properties, however, the furnace is cleaned out and generally becomes more efficient.A technical research paper
describes laboratory research and field trials project using pure biodiesel and biodiesel blends as a heating fuel in oil fired boilers. During the Biodiesel Expo 2006 in the UK, Andrew J. Robertson presented his biodiesel heating oil research from his technical paper and suggested that B20 biodiesel could reduce UK household CO2 emissions by 1.5 million tonnes per year
Historical background
Transesterification of a vegetable oil was conducted as early as 1853 by scientists E. Duffy and J. Patrick, many years before the first diesel engine became functional. Rudolf Diesel's prime model, a single 10 ft (3 m) iron cylinder with a flywheel at its base, ran on its own power for the first time in Augsburg, Germany, on August 10, 1893. In remembrance of this event, August 10 has been declared "International Biodiesel Day".
Rudolf Diesel demonstrated a Diesel engine running on peanut oil (at the request of the French government) built by the French Otto Company at the World Fair in Paris, France in 1900, where it received the Grand Prix (highest prize).
This engine stood as an example of Diesel's vision because it was powered by peanut oil — a biofuel, though not biodiesel, since it was not transesterified. He believed that the utilization of biomass fuel was the real future of his engine. In a 1912 speech Diesel said, "the use of vegetable oils for engine fuels may seem insignificant today but such oils may become, in the course of time, as important as petroleum and the coal-tar products of the present time."
During the 1920s, diesel engine manufacturers altered their engines to utilize the lower viscosity of petrodiesel (a fossil fuel), rather than vegetable oil (a biomass fuel). The petroleum industries were able to make inroads in fuel markets because their fuel was much cheaper to produce than the biomass alternatives. The result, for many years, was a near elimination of the biomass fuel production infrastructure. Only recently, have environmental impact concerns and a decreasing price differential made biomass fuels such as biodiesel a growing alternative.
Despite the widespread use of fossil petroleum-derived diesel fuels, interest in vegetable oils as fuels in internal combustion engines is reported in several countries during the 1920's and 1930's and later during World War II. Belgium, France, Italy, the United Kingdom, Portugal, Germany,
Brazil, Argentina, Japan and China have been reported to have tested and used vegetable oils as diesel fuels during this time. Some operational problems were reported due to the high viscosity of vegetable oils compared to petroleum diesel fuel, which result in poor atomization of the fuel in the fuel spray and often leads to deposits and coking of the injectors, combustion chamber and valves. Attempts to overcome these problems included heating of the vegetable oil, blending it with petroleum-derived diesel fuel or ethanol, pyrolysis and cracking of the oils.
On August 31, 1937, G. Chavanne of the University of Brussels (Belgium) was granted a patent for a "Procedure for the transformation of vegetable oils for their uses as fuels" (fr. 'Procédé de Transformation d’Huiles Végétales en Vue de Leur Utilisation comme Carburants') Belgian Patent 422,877. This patent described the alcoholysis (often referred to as transesterification) of vegetable oils using methanol and ethanol in order to separate the fatty acids from the glycerol by replacing the glycerol by short linear alcohols. This appears to be the first account of the production of what is known as "biodiesel" today.
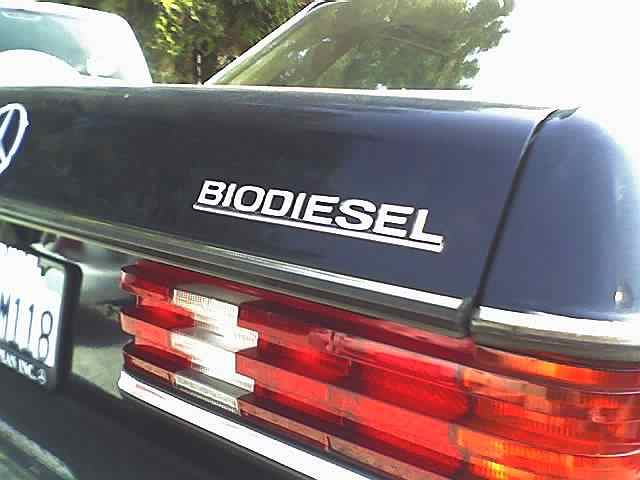
Mercedes
Benz Biodiesel car
More recently, in 1977, Brazilian scientist Expedito Parente produced biodiesel using transesterification with ethanol, and again filed a patent for the same process. This process is classified as biodiesel by international norms, conferring a "standardized identity and quality. No other proposed biofuel has been validated by the motor
industry." Currently, Parente's company Tecbio is working with Boeing and
NASA to certify bioquerosene (bio-kerosene), another product produced and patented by the Brazilian
scientist.
Research into the use of transesterified sunflower oil, and refining it to diesel fuel standards, was initiated in South Africa in 1979. By 1983, the process for producing fuel-quality, engine-tested biodiesel was completed and published
internationally. An Austrian company, Gaskoks, obtained the technology from the South African Agricultural Engineers; the company erected the first biodiesel pilot plant in November 1987, and the first industrial-scale plant in April 1989 (with a capacity of 30,000 tons of rapeseed per annum).
Throughout the 1990s, plants were opened in many European countries, including the Czech Republic, Germany and Sweden. France launched local production of biodiesel fuel (referred to as diester) from rapeseed oil, which is mixed into regular diesel fuel at a level of 5%, and into the diesel fuel used by some captive fleets (e.g. public transportation) at a level of 30%. Renault, Peugeot and other manufacturers have certified truck engines for use with up to that level of partial biodiesel; experiments with 50% biodiesel are underway. During the same period, nations in other parts of the world also saw local production of biodiesel starting up: by 1998, the Austrian Biofuels Institute had identified 21 countries with commercial biodiesel projects. 100% Biodiesel is now available at many normal service stations across
Europe.
In September 2005 Minnesota became the first U.S. state to mandate that all diesel fuel sold in the state contain part biodiesel, requiring a content of at least 2%
biodiesel.
Properties
Biodiesel has better lubricity than that of today's diesel fuels. During the manufacture of these, to comply with low SO2 engine emission limits set in modern standards, severe hydrotreatment is included. Biodiesel addition reduces wear[16] increasing the life of the fuel injection equipment that relies on the fuel for its lubrication, such as high pressure injection pumps, pump injectors (also called unit injectors) and fuel injectors.
Older diesel Mercedes are popular for running on biodiesel.The volumetric energy density of biodiesel is about 33 MJ/l. This is 9 % lower than regular Number 2 petrodiesel. Variations in biodiesel energy density is more dependent on the feedstock used than the production process. Still these variations are less than for
petrodiesel. It has been claimed biodiesel gives better lubricity and more complete combustion thus increasing the engine energy output and partially compensating for the higher energy density of
petrodiesel.
Biodiesel is a liquid which varies in color — between golden and dark brown — depending on the production feedstock. It is immiscible with water, has a high boiling point and low vapor pressure. Typical methyl ester biodiesel has a flash point of ~ 150 °C (300 °F). Biodiesel has a density of ~ 0.88 g/cm³, less than that of water.
Biodiesel has a viscosity similar to petrodiesel, the current industry term for diesel produced from petroleum. Biodiesel has high lubricity and virtually no sulfur content, and it is often used as an additive to Ultra-Low Sulfur Diesel (ULSD) fuel.
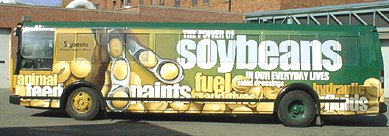
Biodiesel
soybeans powered bus
Technical standards
Biodiesel sampleThe common international standard for biodiesel is EN 14214.
There are additional national specifications. ASTM D6751 is the most common standard referenced in the United States and Canada. In Germany, the requirements for biodiesel are fixed in the DIN EN 14214 standard and in the UK the requirements for biodiesel is fixed in the BS EN 14214 standard, although these last two standards are essentially the same as EN 14214 and are just prefixed with the respective national standards institution codes.
There are standards for three different varieties of biodiesel, which are made of different oils:
RME (rapeseed methyl ester, according to DIN E 51606)
PME (vegetable methyl ester, purely vegetable products, according to DIN E 51606)
FME (fat methyl ester, vegetable and animal products, according to DIN V 51606)
The standards ensure that the following important factors in the fuel production process are satisfied:
Complete reaction.
Removal of glycerin.
Removal of catalyst.
Removal of alcohol.
Absence of free fatty acids.
Low sulfur content.
Basic industrial tests to determine whether the products conform to the standards typically include gas chromatography, a test that verifies only the more important of the variables above. Tests that are more complete are more expensive. Fuel meeting the quality standards is very non-toxic, with a toxicity rating (LD50) of greater than 50
mL/kg.
Gelling
The cloud point, or temperature at which pure (B100) biodiesel starts to gel, varies significantly and depends upon the mix of esters and therefore the feedstock oil used to produce the biodiesel. For example, biodiesel produced from low erucic acid varieties of canola seed (RME) starts to gel at approximately −10 °C (14 °F). Biodiesel produced from tallow tends to gel at around +16 °C (68 °F). As of 2006, there are a very limited number of products that will significantly lower the gel point of straight biodiesel. A number of studies have shown that winter operation is possible with biodiesel blended with other fuel oils including #2 low sulfur diesel fuel and #1 diesel / kerosene. The exact blend depends on the operating environment: successful operations have run using a 65% LS #2, 30% K #1, and 5% bio blend. Other areas have run a 70% Low Sulfur #2, 20% Kerosene #1, and 10% bio blend or an 80% K#1, and 20% biodiesel blend. According to the National Biodiesel Board (NBB), B20 (20% biodiesel, 80% petrodiesel) does not need any treatment in addition to what is already taken with petrodiesel.
Some people modify their vehicles to permit the use of biodiesel without mixing and without the possibility of gelling at low temperatures. This practice is similar to the one used for running straight vegetable oil. They install a second fuel tank (some models of trucks have two tanks already). This second fuel tank is insulated and a heating coil using engine coolant is run through the tank. There is then a temperature sensor installed to notify the driver when the fuel is warm enough to burn, the driver then switches which tank the engine is drawing from.
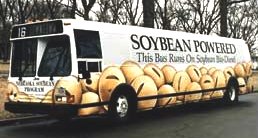
Biodiesel
soybeans bus
Contamination by water
Biodiesel may contain small but problematic quantities of water. Although it is hydrophobic (non-miscible with water molecules), it is said to be, at the same time, hygroscopic to the point of attracting water molecules from atmospheric
moisture; one of the reasons biodiesel can absorb water is the persistence of mono and diglycerides left over from an incomplete reaction. These molecules can act as an emulsifier, allowing water to mix with the
biodiesel. In addition, there may be water that is residual to processing or resulting from storage tank condensation. The presence of
water is a problem because:
Water reduces the heat of combustion of the bulk fuel. This means more smoke, harder starting, less power.
Water causes corrosion of vital fuel system components: fuel pumps, injector pumps, fuel lines, etc.
Water & microbes cause the paper element filters in the system to fail (rot), which in turn results in premature failure of the fuel pump due to ingestion of large particles.
Water freezes to form ice crystals near 0 °C (32 °F). These crystals provide sites for nucleation and accelerate the gelling of the residual fuel.
Water accelerates the growth of microbe colonies, which can plug up a fuel system. Biodiesel users who have heated fuel tanks therefore face a year-round microbe problem.
Previously, the amount of water contaminating biodiesel has been difficult to measure by taking samples, since water and oil separate. However, it is now possible to measure the water content using water in oil sensors.
Additionally, water can cause pitting in the pistons on a diesel engine.
Biodiesel can also be used as a heating fuel in domestic and commercial boilers. and would only require around 330,000 hectares of arable land for the required biodiesel for the UK heating oil sector. The paper also suggests that existing oil boilers can easily and cheaply be converted to biodiesel if B20 biodiesel is used.
Availability and prices
In some countries biodiesel is less expensive than conventional diesel.For more details on this topic, see Biodiesel around the World.
Global biodiesel production reached 3.8 million tons in 2005. Approximately 85% of biodiesel production came from the European Union.
In the United States, average retail (at the pump) prices, including Federal and state motor taxes, of B2/B5 are lower than petroleum diesel by about 12 cents, and B20 blends are the same as petrodiesel. [20] B99 and B100 generally cost more than petrodiesel except where local governments provide a subsidy.
Production
Chemically, transesterified biodiesel comprises a mix of mono-alkyl esters of long chain fatty acids. The most common form uses methanol (converted to sodium methoxide) to produce methyl esters as it is the cheapest alcohol available, though ethanol can be used to produce an ethyl ester biodiesel and higher alcohols such as isopropanol and butanol have also been used. Using alcohols of higher molecular weights improves the cold flow properties of the resulting ester, at the cost of a less efficient transesterification reaction. A lipid transesterification production process is used to convert the base oil to the desired esters. Any Free fatty acids (FFAs) in the base oil are either converted to soap and removed from the process, or they are esterified (yielding more biodiesel) using an acidic catalyst. After this processing, unlike straight vegetable oil, biodiesel has combustion properties very similar to those of petroleum diesel, and can replace it in most current uses.
A byproduct of the transesterification process is the production of glycerol. For every 1 tonne of biodiesel that is manufactured, 100 kg of glycerol are produced. Originally, there was a valuable market for the glycerol, which assisted the economics of the process as a whole. However, with the increase in global biodiesel production, the market price for this crude glycerol (containing 20% water and catalyst residues) has crashed. Research is being conducted globally to use this glycerol as a chemical building block. One initiative in the UK is The Glycerol Challenge.
Usually this crude glycerol has to be purified, typically by performing vacuum distillation. This is rather energy intensive. The refined glycerol (98%+ purity) can then be utilised directly, or converted into other products. The following announcements were made in 2007: A joint venture of Ashland Inc. and Cargill announced plans to make propylene glycol in Europe from
glycerol and Dow Chemical announced similar plans for North America. Dow also plans to build a plant in China to make epichlorhydrin from
glycerol. Epichlorhydrin is a raw material for epoxy resins.
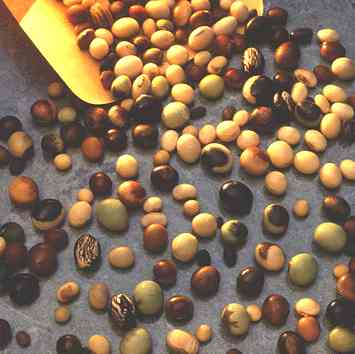
Soybeans are used as a source of
biodiesel plant oils
Biodiesel feedstocks - plant oils
Types
Vegetable fats (list)
Essential oil (list)
Macerated (list)
Uses
Drying oil - Oil paint
Cooking oil
Fuel - Biodiesel
Aromatherapy
Components
Saturated fat
Monounsaturated fat
Polyunsaturated fat
Trans fat
A variety of oils can be used to produce biodiesel. These include:
Virgin oil feedstock; rapeseed and soybean oils are most commonly used, soybean oil alone accounting for about ninety percent of all fuel stocks in the US. It also can be obtained from field pennycress and Jatropha other crops such as mustard, flax, sunflower, palm oil, hemp.
Waste vegetable oil (WVO);
Animal fats including tallow, lard, yellow grease, chicken fat, and the by-products of the production of Omega-3 fatty acids from fish oil.
Algae, which can be grown using waste materials such as
sewage and without displacing land currently used for food production.
Many advocates suggest that waste vegetable oil is the best source of oil to produce biodiesel, but since the available supply is drastically less than the amount of petroleum-based fuel that is burned for transportation and home heating in the world, this local solution does not scale well.
Animal fats are similarly limited in supply, and it would not be efficient to raise animals simply for their fat. However, producing biodiesel with animal fat that would have otherwise been discarded could replace a small percentage of petroleum diesel usage. Currently, a 5-million dollar plant is being built in the USA, with the intent of producing 11.4 million litres (3 million gallons) biodiesel from some of the estimated 1 billion kg (2.3 billion pounds) of
chicken fat produced annually the local Tyson poultry plant.
Quantity of feedstocks required
Worldwide production of vegetable oil and animal fat is not yet sufficient to replace liquid fossil fuel use. Furthermore, some object to the vast amount of farming and the resulting fertilization, pesticide use, and land use conversion that would be needed to produce the additional vegetable oil. The estimated transportation diesel fuel and home heating oil used in the United States is about 160 million tonnes (350 billion pounds) according to the Energy Information Administration, US Department of Energy. In the United States, estimated production of vegetable oil for all uses is about 11 million tonnes (24 billion pounds) and estimated production of animal fat is 5.3 million tonnes (12 billion
pounds).
If the entire arable land area of the USA (470 million acres, or 1.9 million square kilometers) were devoted to biodiesel production from soy, this would just about provide the 160 million tonnes required (assuming an optimistic 98 gpa of biodiesel). This land area could in principle be reduced significantly using algae, if the obstacles can be overcome. The US DOE estimates that if algae fuel replaced all the petroleum fuel in the United States, it would require 15,000 square miles (38,849 square kilometers), which is a few thousand square miles larger than Maryland, or 1.3
Belgiums. The advantages of algae are that it can be grown on non-arable land or in marine environments, and the potential oil yields are much higher than from plants.
Yield
Feedstock yield efficiency per acre affects the feasibility of ramping up production to the huge industrial levels required to power a significant percentage of national or world vehicles. Some typical yields in US gallons of biodiesel per acre are:
Algae fuel yields have not yet been accurately determined, but DOE is reported as saying that algae yield 30 times more energy per acre than land crops such as
soybeans, and some estimate even higher yields up to 15000 gpa.
The Jatropha plant has been cited as a high-yield source of biodiesel but such claims have also been exaggerated. The more realistic estimates put the yield at about 200 gpa (1.5-2 tonnes per
hectare). It is grown in the Philippines, Mali and India, is drought-resistant, and can can share space with other cash crops such as
coffee, sugar, fruits and
vegetables.
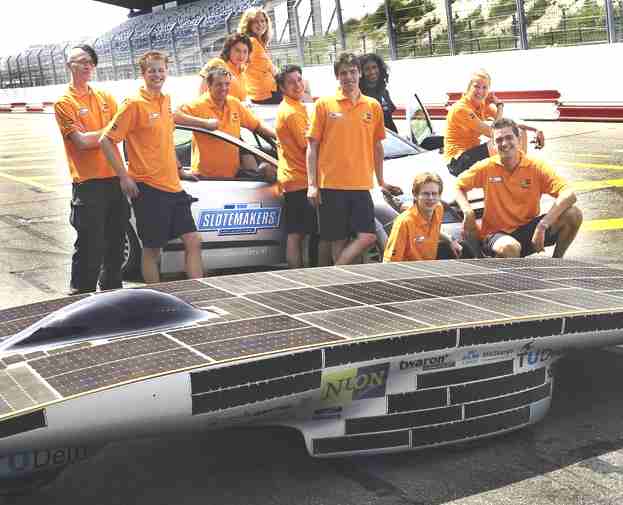
Solar
cells convert energy at around 15% - much more efficient
Nuna
3 racing car and team members,
Netherlands
Efficiency and economic arguments
According to a study written by Drs. Van Dyne and Raymer for the Tennessee Valley Authority, the average US farm consumes fuel at the rate of 82 litres per hectare (8.75 US gallons per acre) of land to produce one crop. However, average crops of rapeseed produce oil at an average rate of 1,029 L/ha (110 US gal/acre), and high-yield rapeseed fields produce about 1,356 L/ha (145 US gal/acre). The ratio of input to output in these cases is roughly 1:12.5 and 1:16.5. Photosynthesis is known to have an efficiency rate of about 3-6% of total solar
radiation and if the entire mass of a crop is utilized for energy production, the overall efficiency of this chain is currently about
1%. While this may compare favorably to solar cells combined with an
electric drive train, biodiesel is less costly to deploy (solar cells cost approximately US$1,000 per square meter) and transportation (electric vehicles require batteries which currently have a much lower energy density than liquid fuels).
However, these statistics by themselves are not enough to show whether such a change makes economic sense. Additional factors must be taken into account, such as: the fuel equivalent of the energy required for processing, the yield of fuel from raw oil, the return on cultivating food, the effect biodiesel will have of food prices and the relative cost of biodiesel versus petrodiesel.
The debate over the energy balance of biodiesel is ongoing. Transitioning fully to biofuels could require immense tracts of land if traditional food crops are used (although non food crops can be utilized). The problem would be especially severe for nations with large economies, since energy consumption scales with economic
output.
If using only traditional food plants, most such nations do not have sufficient arable land to produce biofuel for the nation's vehicles. Nations with smaller economies (hence less energy consumption) and more arable land may be in better situations, although many regions cannot afford to divert land away from food production.
For third world countries, biodiesel sources that use marginal land could make more sense, e.g. honge oil
nuts grown along roads or jatropha grown along rail lines. More recent studies using a species of algae with up to 50% oil content have concluded that only 28,000 km² or 0.3% of the land area of the US could be utilized to produce enough biodiesel to replace all transportation fuel the country currently
utilizes. Furthermore, otherwise unused desert land (which receives high
solar radiation) could be most effective for growing the algae, and the algae could utilize farm waste and excess CO2 from factories to help speed the growth of the
algae.
In tropical regions, such as Malaysia and Indonesia, oil palm is being planted at a rapid pace to supply growing biodiesel demand in Europe and other markets. It has been estimated in Germany that palm oil biodiesel has less than 1/3 the production costs of rapeseed
biodiesel. The direct source of the energy content of biodiesel is solar energy captured by plants during photosynthesis. Regarding the positive energy balance of
biodiesel:
When straw was left in the field, biodiesel production was strongly energy positive, yielding 1 GJ biodiesel for every 0.561 GJ of energy input (a yield/cost ratio of 1.78).
When straw was burned as fuel and oilseed rapemeal was used as a fertilizer, the yield/cost ratio for biodiesel production was even better (3.71). In other words, for every unit of energy input to produce biodiesel, the output was 3.71 units (the difference of 2.71 units would be from solar energy).
Biodiesel is becoming of interest to companies interested in commercial scale production as well as the more usual home brew biodiesel user and the user of straight vegetable oil or waste vegetable oil in diesel engines. Homemade biodiesel processors are many and varied.
Environmental effects
Calculation of Carbon Intensity of Soy biodiesel grown in the US and burnt in the UK, using UK government calculation
Graph of UK figures for the Carbon Intensity of Biodiesels and fossil fuels. This graph assumes that all biodiesels are burnt in their country of
origin
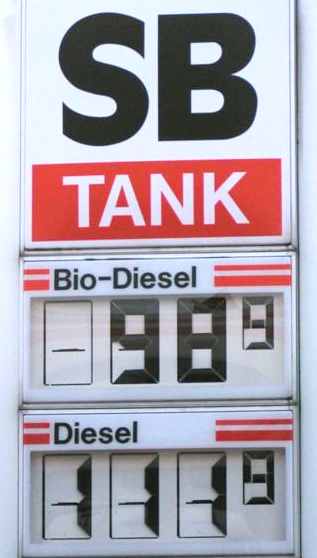
Biodiesel
Vs Diesel fuel pump prices
Carbon Dioxide production
Making and burning Biodiesel contributes to atmospheric carbon dioxide to a smaller extent than burning fossil fuels. The calculation of exactly how much
Carbon Dioxide is produced is a complex and inexact process, and is highly dependant on the method by which the biofuel is produced and the assumptions made in the calculation. A calculation should include:
-
The cost of growing the feedstock
-
The cost of transporting the feedstock to the factory
-
The cost of processing the feedstock into biodiesel
Such a calculation may or may not consider the following effects:
-
The cost of the change in land use of the area where the fuel feedstock is grown.
-
The cost of transportation of the biodiesel from the factory to its point of use
-
The efficiency of the biodiesel compared with standard diesel
-
The amount of Carbon Dioxide produced at the tail pipe. (Biodiesel can produce 4.7% more)
-
The benefits due to the production of useful bi-products, such as cattle feed or glycerine
-
The graphs on the right shows figures calculated by the UK government for the purposes of the Renewable transport fuel
obligation
Pollution
Biodiesel contains fewer aromatic hydrocarbons: benzofluoranthene: 56% reduction; Benzopyrenes: 71%
reduction.
Biodiesel can reduce by as much as 20% the direct (tailpipe) emission of particulates, small particles of solid combustion products, on
vehicles with particulate filters, compared with low-sulfur (<50 ppm) diesel. Particulate emissions as the result of production are reduced by around 50%, compared with fossil-sourced diesel. (Beer et al, 2004).
Biodiesel has a higher cetane rating than petrodiesel, which can improve performance and clean up emissions compared to crude petro-diesel (with cetane lower than 40).
Biodegradable
Biodiesel is considered readily biodegradable under ideal conditions and non-toxic. A University of Idaho study compared biodegradation rates of biodiesel, neat vegetable oils, biodiesel and petroleum diesel blends, and neat 2-D diesel fuel. Using low concentrations of the product to be degraded (10 ppm) in nutrient and sewage sludge amended solutions, they demonstrated that biodiesel degraded at the same rate as a dextrose control and 5 times as quickly as petroleum diesel over a period of 28 days, and that biodiesel blends doubled the rate of petroleum diesel degradation through co-metabolism. The same study examined soil degradation using 10 000 ppm of biodiesel and petroleum diesel, and found biodiesel degraded at twice the rate of petroleum diesel in soil. In all cases, it was determined biodiesel also degraded more completely than petroleum diesel, which produced poorly degradable undetermined intermediates. Toxicity studies for the same project demonstrated no mortalities and few toxic effects on rats and rabbits with up to 5000 mg/kg of biodiesel. Petroleum diesel showed no mortalities at the same concentration either, however toxic effects such as hair loss and urinary discolouring were noted with concentrations of >2000 mg/l in rabbits.
Nontoxic to humans
In the United States, biodiesel is the only alternative fuel to have successfully completed the Health Effects Testing requirements (Tier I and Tier II) of the Clean Air Act (1990).
Since biodiesel is more often used in a blend with petroleum diesel, there are fewer formal studies about the effects on pure biodiesel in unmodified engines and vehicles in day-to-day use. Fuel meeting the standards and engine parts that can withstand the greater solvent properties of biodiesel is expected
to - and in reported cases does - run without any additional problems than the use of petroleum diesel.
Flammability
The flash point of biodiesel (>150 °C) is significantly higher than that of petroleum diesel (64 °C) or gasoline (−45 °C). The gel point of biodiesel varies depending on the proportion of different types of esters contained. However, most biodiesel, including that made from soybean oil, has a somewhat higher gel and cloud point than petroleum diesel. In practice this often requires the heating of storage tanks, especially in cooler climates.
Pure biodiesel (B100) can be used in any petroleum diesel engine, though it is more commonly used in lower concentrations. Some areas have mandated ultra-low sulfur petrodiesel, which reduces the natural viscosity and lubricity of the fuel due to the removal of sulfur and certain other materials. Additives are required to make ULSD properly flow in engines, making biodiesel one popular alternative. Ranges as low as 2% (B2) have been shown to restore lubricity. Many municipalities have started using 5% biodiesel (B5) in snow-removal equipment and other systems.
Food vs fuel
Food quality vegetable oil has become so expensive there is no longer a profit viability for its use. Food grade vegetable oil pricing is on a similar upward ramp as food in general. Accessing food stuffs in poor countries has always been problematic for the inhabitants. Non food grade vegetable feed stocks are under use or consideration for use to make biodiesel and have been so during the entire history of biodiesel.
In some poor countries the rising price of vegetable oil is causing problems.
There are those that say using a food crop for fuel sets up competition between food in poor countries and fuel in rich countries. Some propose that fuel only be made from non-edible vegetable oils like jatropha oil. Others argue that the problem is more fundamental. Farmers can switch from producing food crops to producing biofuel crops to make more money, even if the new crops are not edible.
The law of supply and demand predicts that if less farmers are producing food the price of food will rise. It may take some time, as farmers can take some time to change which things they are growing, but increasing demand for biofuels is likely to result in price increases for many kinds of food. Some have pointed out that there are poor farmers and poor countries making more money because of the higher price of vegetable oil.
Environmental concerns
The locations where oil-producing plants are grown is of increasing concern. Mono-culture plantations clear cut large areas of tropical forest in order to grow such oil rich crops such as oil palm. In the Philippines and Indonesia such forest clearing is already underway for the production of palm oil. In Indonesia, for example, deforestation has caused displacement of indigenous peoples. Also, in some areas use of pesticides for biofuel crops are disrupting clean water
supplies. Loss of habitat on such a scale could endanger numerous species of plants and animals. A particular concern which has received considerable attention is the threat to the already-shrinking populations of orangutans on the Indonesian islands of Borneo and Sumatra, which face possible
extinction.
Third world production
Biodiesel and feedstock oils produced in Asia, South America and Africa are currently less expensive than those produced in Europe and North America suggesting that imports to these wealthier nations are likely to increase in future. Like all petroleum based fuels, biodiesel also requires a significant investment of energy before it arrives at petrol pumps, thus fair comparisons among fuels require full lifecycle analyses for each fuel type. If deforestation, and monoculture farming techniques were used to grow biofuel crops, biodiesel is predicted to become a serious threat to the environment. These problems could be exacerbated as biodiesel becomes more popular unless stringent laws are introduced and enforced to control biodiesel production. Non-food energy crops and lipid rich algaes with vastly greater oil yields may also replace low-yield annual food crops such as soybeans, skirting the deforestation risk associated with widespread uptake of biodiesel.GuJi
As non-food crops also facilitate the use of degraded lands, wastewater, processed sewage, and other waste streams, the benefits of such crops go well beyond their greater
yields. Moreover, select non-food crops such as jatropha and castorbean can be grown in polycultures, in non-till agricultural applications, and they scale well from the standpoint of production, storage, and processing. As such, these crops might benefit small-scale farmers throughout tropical and temperate latitudes, providing a cash crop option which can also displace local demand for imported
petroleum.
NOx emissions
If burned without additives, Biodiesel (B100) is estimated to produce about 10% more nitrogen oxide NOx tailpipe-emissions than petrodiesel. As biodiesel has a low sulfur content, NOx emissions can be reduced through the use of catalytic converters to less than the NOx emissions from conventional diesel engines. Moreover, as a transportation fuel, biodiesel is in its infancy in terms of additives which are capable of improving energy density, resistance to gelling, and NOx emissions. Debate continues over NOx, particulates, smog, and greenhouse gas emissions from biodiesel and all other new transportation fuels, biofuels in particular. Ultimately, greater clarity on the fundamental distinctions between smog and other local pollution issues vs. greenhouse gas emissions will be essential for both well founded public policy as well as well informed consumer choices. In February 2006 a Navy biodiesel expert claimed NOx emissions in practice were actually lower than baseline. Further research is needed.
Recent advances in the use of cerium oxide help eliminate NOx emissions from both petrodiesel and
biodiesel, and diesel fuel additives based on cerium oxide can improve fuel consumption by 11%[citation needed] in unmodified diesel engines.
Current research
There is ongoing research into finding more suitable crops and improving oil yield. Using the current yields, vast amounts of land and fresh water would be needed to produce enough oil to completely replace fossil fuel usage. It would require twice the land area of the US to be devoted to soybean production, or two-thirds to be devoted to rapeseed production, to meet current US heating and transportation
needs.
Specially bred mustard varieties can produce reasonably high oil yields, and have the added benefit that the meal leftover after the oil has been pressed out can act as an effective and biodegradable
pesticide.
Algaculture
From 1978 to 1996, the U.S. National Renewable Energy Laboratory experimented with using algae as a biodiesel source in the "Aquatic Species
Program". A self-published article by Michael Briggs, at the UNH Biodiesel Group, offers estimates for the realistic replacement of all vehicular fuel with biodiesel by utilizing algae that have a natural oil content greater than 50%, which Briggs suggests can be grown on algae ponds at wastewater treatment
plants. This oil-rich algae can then be extracted from the system and processed into biodiesel, with the dried remainder further reprocessed to create ethanol.
The production of algae to harvest oil for biodiesel has not yet been undertaken on a commercial scale, but feasibility studies have been conducted to arrive at the above yield estimate. In addition to its projected high yield, algaculture
- unlike crop-based biofuels - does not entail a decrease in food production, since it requires neither farmland nor fresh water. Some
companies are pursuing algae bio-reactors for various purposes, including biodiesel production.
On May 11, 2006 the Aquaflow Bionomic Corporation in Marlborough, New Zealand announced that it had produced its first sample of bio-diesel fuel made from algae found in sewage
ponds. Unlike previous attempts, the algae was naturally grown in pond discharge from the Marlborough District Council's sewage treatment works.
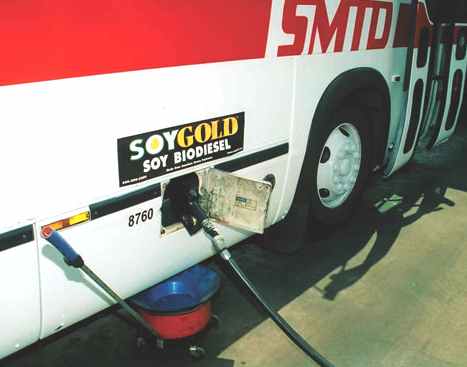
LINKS
and REFERENCE
-
Biodiesel
101 - Biodiesel Definitions.
National Biodiesel Board.
-
Knothe,
G.. Historical
Perspectives on Vegetable Oil-Based Diesel Fuels (PDF). INFORM,
Vol. 12(11), p. 1103-1107 (2001).
-
McCormick,
R.L.. 2006
Biodiesel Handling and Use Guide Third Edition (PDF).
-
Kemp,
William. Biodiesel: Basics and Beyond. Canada: Aztext Press, 2006.
-
http://nbb.grassroots.com/07Releases/Incentive/
-
First
UK biodiesel train launched. BBC.
-
Soviet-era
training jet flies on biodiesel
-
Virgin
Atlantic to Run Bio-diesel Test Flight
-
Biofuel-powered
jet to make test flight
-
Robertson,
Andrew. Biodiesel
Heating Oil: Sustainable Heating for the future. Institute of
Plumbing and Heating Engineering.
-
biodiesel.org
report 246
-
[1]
Quote from Tecbio website
-
[2]
O Globo newspaper interview in Portuguese]
-
SAE
Technical Paper series no. 831356. SAE International Off Highway
Meeting, Milwaukee, Wisconsin, USA, 1983
-
[3]
Minnesota regulations on biodiesel content
-
http://www.biodiesel.org/pdf_files/fuelfactsheets/Lubricity.PDF
-
National
Biodiesel Board (2005-10). "Energy
Content".
-
http://www.unh.edu/p2/biodiesel/article_alge.html
-
UFOP
- Union zur Förderung von Oel. Biodiesel
FlowerPower: Facts * Arguments * Tips (PDF)
-
http://www.eere.energy.gov/afdc/pdfs/afpr_jul_07.pdf
-
http://www.dow.com/propyleneglycol/news/20070315b.htm
-
http://epoxy.dow.com/epoxy/news/2007/20070326b.htm
-
Leonard,
Christopher. "Not
a Tiger, but Maybe a Chicken in Your Tank", Washington
Post, Associated Press
-
Errol
Kiong. "NZ
firm makes bio-diesel from sewage in world first", The New
Zealand Herald
-
Biodiesel
from Animal Fat. E85.whipnet.net.
-
http://tonto.eia.doe.gov/dnav/pet/pet_cons_821dst_dcu_nus_a.htm)
-
Van
Gerpen, John (2004 - 07). Business
Management for Biodiesel Producers, August 2002 - January 2004.
National Renewable Energy Laboratory.
-
A
Promising Oil Alternative: Algae Energy - washingtonpost.com
-
Biofuels:
some numbers
-
[www.ces.purdue.edu/extmedia/ID/ID-337.pdf
Purdue report ID-337]
-
Biodiesel
Yields Even Higher Energy Balance
-
DOE
quoted by Washington Post in "A Promising Oil Alternative: Algae
Energy"
-
Thomas
F. Riesing, Ph.D. (Spring 2006). Algae
for Liquid Fuel Production. Oakhaven Permaculture Center
-
India's
jatropha plant biodiesel yield termed wildly exaggerated
-
Jatropha
for biodiesel
-
Kazuhisa
Miyamoto (1997). "Renewable
biological systems for alternative sustainable energy production (FAO
Agricultural Services Bulletin - 128)" (HTML). Final. FAO
- Food and Agriculture Organization of the United Nations
-
Tad
Patzek Thermodynamics
of the Corn-Ethanol Biofuel Cycle (section 3.11 Solar Energy Input
into Corn Production) (PDF). Berkeley; Critical Reviews in Plant
Sciences, 23(6):519-567 (2004).
-
Looking
Forward: Energy and the Economy (PDF).
-
Hands
On: Power Pods - India.
-
Michael
Briggs (August 2004). Widescale
Biodiesel Production from Algae. UNH Biodiesel Group (University
of New Hampshire).
-
Palm
Oil Based Biodiesel Has Higher Chances Of Survival.
-
Graph
derived from information found in UK government document.Carbon
and Sustainability Reporting Within the Renewable Transport Fuel
Obligation
-
Carbon
and Sustainability Reporting Within the Renewable Transport Fuel
Obligation
-
University
Of Idaho bioenergy
-
http://www.abc.net.au/news/stories/2007/07/19/1982450.htm
-
The
other oil shock: Vegetable oil prices soar - International Herald
Tribune
-
Food
versus fuel debate escalates
-
How
Food and Fuel Compete for Land by Lester Brown - The Globalist >
> Global Energy
-
The
Economist – The End Of Cheap Food.
-
Biofuel
demand leading to human rights abuses, report claims Jessica
Aldred, guardian.co.uk
-
Helen
Buckland, Ed Matthew "The
Oil for Ape Scandal: How palm oil is threatening the orang-utan"
(PDF (458 Kb)). Summary. Friends of the Earth Trust.
-
Catherine
Foster New
catalyst helps eliminate NOx from diesel exhaust (HTML). Argonne
National Laboratory.
-
John
Sheehan, Terri Dunahay, John Benemann, Paul Roessler (July 1998).
"A
look back at the U.S. Department of Energy's Aquatic Species Program:
Biodiesel from Algae" (PDF (3.7 Mb)). Close-out Report.
United States Department of Energy.
-
An
Overview of Biodiesel and Petroleum Diesel Lifecycles, May 1998,
Sheehan, et al. NREL (60pp
pdf file)
-
Business
Management for Biodiesel Producers, January 2004, Jon Von Gerpen,
Iowa State University under contract with the National Renewable
Energy Laboratory (NREL) (210pp
pdf file)
-
Energy
balances in the growth of oilseed rape for biodiesel and of wheat for
bioethanol, June 2000, I.R. Richards
-
Life
Cycle Inventory of Biodiesel and Petroleum Diesel for Use in an Urban
Bus, 1998, Sheehan, et al. NREL (314pp
pdf file)
-
Algae
- like a breath mint for smokestacks Mark Clayton, Christian
Science Monitor
-
McCormick,
R.L.. "2006
Biodiesel Handling and Use Guide Third Edition".
-
Biodiesel's
Bright Future from the July-August issue of THE FUTURIST magazine.
-
Biodiesel
at the Open Directory Project
-
European
Biodiesel Board website - European Biodiesel Industry.
-
Renewable
raw materials: Biodiesel leads to more rape (rapeseed) cultivation
-
UNH
Biodiesel Group's comparison of Biodiesel vs. Hydrogen
-
Biodiesel.org
-
Collaborative
Biodiesel Tutorial
-
Oliomap.com
The Global Vegetable Fuel Resources Map

New
energy drinks for performers
..
Thirst for Life
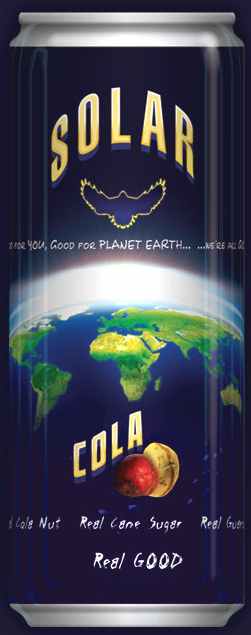
330ml
Earth can - the World in Your Hands
|